The Comprehensive Guide to Plastic Injection Molding for Metal Fabricators
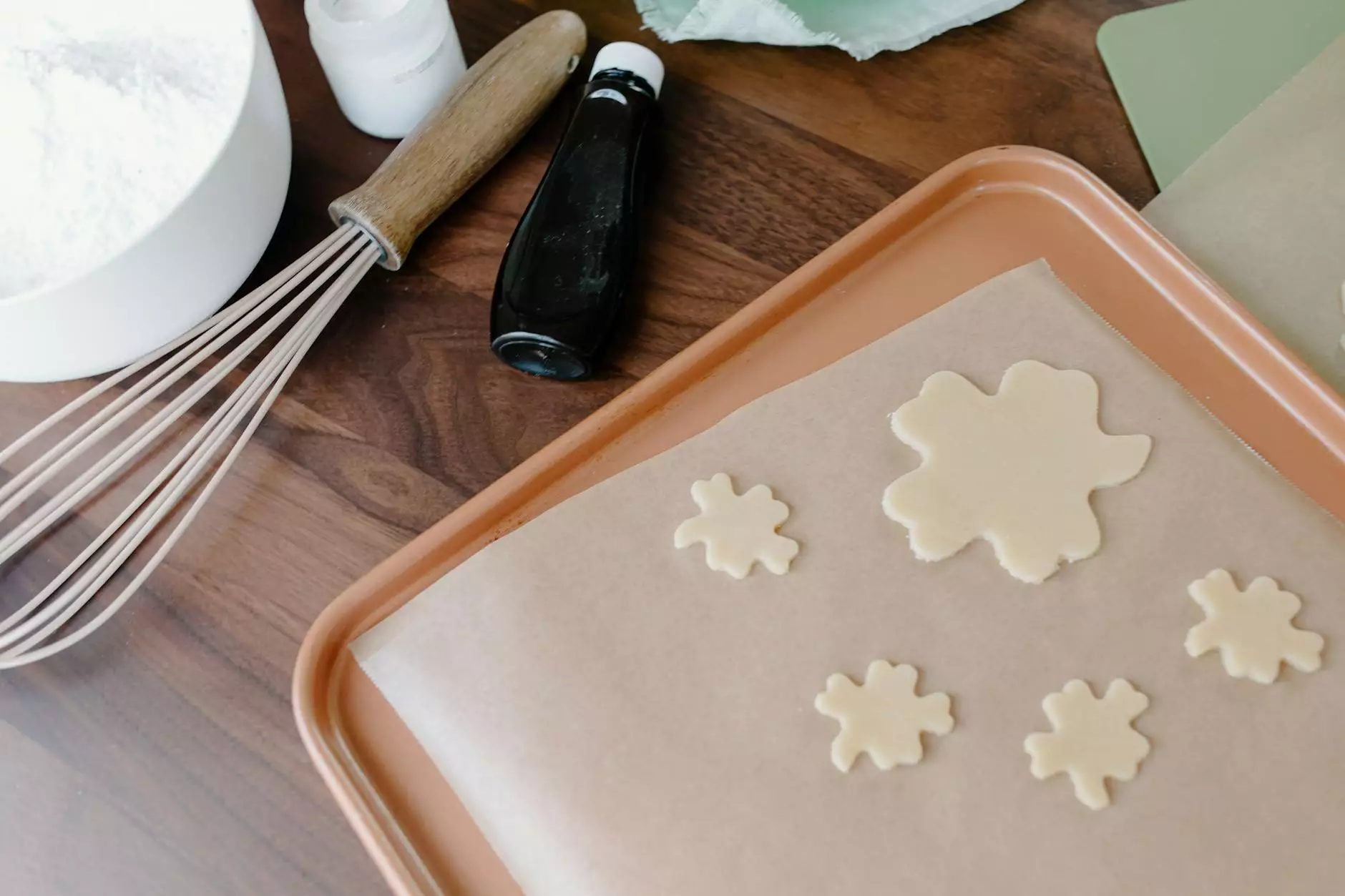
Plastic injection molding is a pivotal manufacturing process that allows businesses, especially metal fabricators, to create high-quality components with precision and efficiency. In today's fast-paced industrial world, understanding the intricacies of this process can significantly enhance a fabricator's capability to deliver top-notch products. Throughout this article, we will delve into the fundamentals of plastic injection molding, explore its advantages for metal fabrication, and provide insights on maximizing its potential within your operations.
What is Plastic Injection Molding?
Plastic injection molding is a manufacturing technique used to produce parts by injecting molten plastic into a mold. The process consists of three main stages: heating, injection, and cooling. This method is celebrated for its ability to create highly complex shapes, maintain precision tolerances, and ensure a high throughput of parts, making it an ideal choice for high-volume production.
The Injection Molding Process Explained
The process of plastic injection molding can be delineated into several key steps:
- Material Selection: The first step involves selecting the appropriate plastic material suited for the intended application, such as thermoplastics or thermosetting plastics.
- Mold Design: Designing the mold is critical. A well-designed mold ensures smooth operation and high-quality output. Factors like cooling channels, venting, and ejection systems must be considered.
- Heating: The plastic material is heated until it reaches a molten state, allowing it to flow easily into the mold.
- Injection: The molten plastic is injected into the mold under high pressure, ensuring every cavity is filled efficiently.
- Cooling: Once the mold is filled, it is allowed to cool. As the plastic cools, it solidifies, taking the shape of the mold.
- Ejection: After cooling, the molded part is ejected from the mold, completing the cycle.
Advantages of Plastic Injection Molding for Metal Fabricators
For metal fabricators looking to diversify their product lines and enhance operational efficiency, plastic injection molding offers numerous advantages:
- High Efficiency: The automated nature of injection molding allows for rapid production rates while minimizing manual labor.
- Cost-Effectiveness: Once a mold is created, the cost per unit decreases significantly with higher production volumes.
- Complex Shapes: Injection molding is capable of producing intricate designs that might be difficult or impossible to achieve with traditional metalworking techniques.
- Material Versatility: A wide range of plastic materials can be used, enabling fabricators to choose materials that meet specific performance requirements.
- Consistent Quality: The reproducibility of the injection molding process results in consistent part quality, reducing defects and waste materials.
Applications of Plastic Injection Molding in Metal Fabrication
Metal fabricators can leverage plastic injection molding across various applications. Some notable uses include:
1. Prototyping
Rapid prototyping using injection molding allows metal fabricators to create test parts quickly, facilitating better design iterations and accelerated product development cycles.
2. Functional Parts Production
Creating end-use parts that require lightweight yet durable materials, such as housings, brackets, and clips, is achievable through injection molding.
3. Assembly Components
Plastic components that need to be easily attached or integrated with metal parts benefit from the precise fit and finish that injection molding provides.
4. Custom Parts for Specific Industries
Industries such as automotive, aerospace, and healthcare require bespoke applications, and injection molding enables the customization needed for regulatory compliance and performance standards.
Choosing the Right Equipment for Plastic Injection Molding
To maximize the benefits of plastic injection molding, selecting the appropriate equipment is crucial. Here are some key considerations:
1. Injection Molding Machines
Investing in a high-quality injection molding machine that suits your production volume and part complexity is essential. Evaluate factors like machine size, clamping force, and injection speed.
2. Molds
The quality of the mold directly affects production efficiency and part quality. Collaborate with experienced mold makers who can provide durable and precisely engineered molds, taking into account material flow and cooling aspects.
3. Auxiliary Equipment
Having auxiliary equipment, such as chillers, robots for part removal, and grinders for reclaiming scrap plastic, can further optimize the molding process and reduce overall costs.
Quality Control in Plastic Injection Molding
One of the most critical aspects of the plastic injection molding process is maintaining strict quality control. Here are some effective strategies:
- Utilizing Advanced Monitoring Systems: Implement real-time monitoring technologies to detect any anomalies during the injection process.
- Regularly Calibrating Machines: Routine calibration ensures machines operate within specified tolerances, maintaining consistent part quality.
- Conducting Material Testing: Perform tests on resin batches to ensure they meet performance specifications and standards.
- Implementing Statistical Process Control: This technique utilizes data collection and analysis to monitor production processes, leading to continuous improvements and waste reduction.
Environmental Considerations in Plastic Injection Molding
As sustainability becomes increasingly important, metal fabricators must consider the environmental impact of plastic injection molding. Strategies to minimize this impact include:
1. Recycling Waste Materials
Incorporating systems to capture and recycle scrap materials from the injection molding process can significantly reduce waste and lower raw material costs.
2. Using Sustainable Materials
Choosing biodegradable plastics or recycled materials for production can help companies meet sustainability goals while fulfilling customer demands for eco-friendly products.
3. Energy Efficiency
Upgrading older machinery with energy-efficient models can drastically reduce energy consumption during the injection molding process.
Conclusion: Embracing the Future of Plastic Injection Molding
In conclusion, plastic injection molding offers immense potential for metal fabricators looking to innovate and expand their capabilities. By understanding the intricacies of the process, investing in the appropriate technology, and implementing robust quality control measures, businesses can not only enhance their production efficiency but also deliver high-quality products that meet market demands. As industries evolve, embracing modern manufacturing techniques such as injection molding will undoubtedly position fabricators for success in an increasingly competitive landscape.
For more information on how to integrate plastic injection molding into your operations, and explore other services that enhance your business capabilities, visit DeepMould.net.
plastic injection molder