Understanding Titanium Fastener Manufacturers
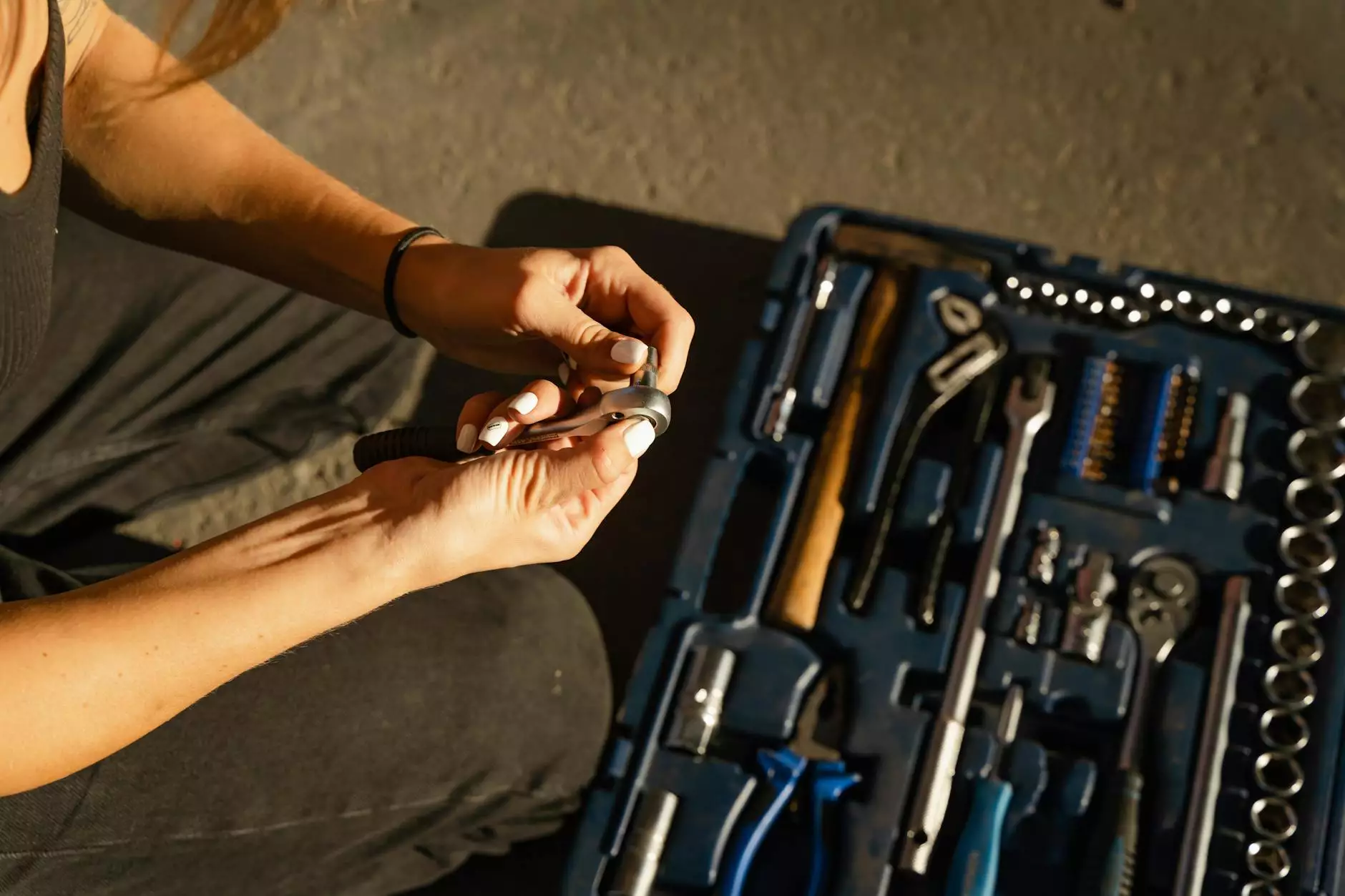
The manufacturing of titanium fasteners has emerged as a critical component in several high-performance industries, including aerospace, automotive, and construction. In this article, we will explore the pivotal role that titanium fastener manufacturers play in these sectors, their advantages, applications, and the future of titanium fasteners in general contracting and beyond.
What Are Titanium Fasteners?
Titanium fasteners, which include bolts, nuts, screws, and washers, are made from titanium or titanium alloys. The unique properties of titanium, such as its high strength-to-weight ratio, corrosion resistance, and biocompatibility, make it an ideal material for applications where durability and reliability are paramount.
Key Properties of Titanium
- Corrosion Resistance: Titanium is highly resistant to corrosion in a variety of environments, making it suitable for chemical and marine applications.
- Low Density: Titanium's lower density compared to steel results in lighter fasteners without sacrificing strength.
- High Strength: Titanium fasteners possess excellent tensile and yield strength, which makes them ideal for high-stress applications.
- Biocompatibility: Titanium is non-toxic and does not cause adverse reactions, making it suitable for medical applications.
The Role of Titanium Fastener Manufacturers
Titanium fastener manufacturers are at the forefront of producing fasteners that meet the stringent requirements of various industries. Their role can be understood through several key functions:
1. Design and Engineering
The manufacturing process begins with design and engineering. Manufacturers work closely with engineers to develop fasteners that meet specific standards and requirements. This collaboration often involves:
- Prototyping: Creating prototypes to test the design's functionality and fit.
- Material Selection: Choosing the right titanium alloy based on the application's needs.
- Stress Testing: Ensuring that fasteners can withstand operational stresses and strains.
2. High-Precision Manufacturing
Once the design is finalized, manufacturers utilize advanced technology to produce titanium fasteners with high precision. This process typically includes:
- CNC Machining: Computer Numerical Control (CNC) machines provide accuracy and repeatability in fastener production.
- Cold Heading: A process that forms the bolt heads and other features at room temperature, enhancing the material's strength.
- Quality Control: Rigorous testing ensures that fasteners meet industry specifications and quality standards.
3. Custom Solutions
Many industries require custom fastener solutions tailored to specific projects. Titanium fastener manufacturers often offer:
- Customized Designs: Creating fasteners according to unique specifications and dimensions.
- Special Coatings: Adding coatings to enhance corrosion resistance or for aesthetic purposes.
- Pre-Assembly Services: Offering pre-assembled fasteners to streamline assembly processes for contractors.
The Importance of Titanium Fasteners in General Contracting
In general contracting, titanium fasteners serve critical roles due to their mechanical properties and reliability. Here’s why general contractors prefer titanium fasteners for their projects:
1. Enhancing Structural Integrity
With the increasing emphasis on safety and durability in construction, utilizing titanium fasteners enhances the overall structural integrity of buildings and infrastructure. Their strength ensures that joints can handle greater loads and stresses.
2. Durability in Harsh Conditions
General contractors often face projects in challenging environments. Titanium fasteners resist corrosion from chemicals, saltwater, and extreme weather conditions, ensuring longevity and performance without frequent replacements.
3. Weight Savings
In the construction industry, reducing the weight of materials without compromising strength leads to lower transportation costs and easier handling onsite. Titanium fasteners are significantly lighter than conventional steel fasteners, making them preferable for many applications.
Applications of Titanium Fasteners
The versatility of titanium fasteners allows them to be used across various sectors. Here are some notable applications:
Aerospace Industry
In aerospace, weight reduction is critical for fuel efficiency and payload capacity. Titanium fasteners are extensively used in aircraft structures, engines, and landing gear. Their high strength and resistance to extreme temperatures make them ideal for this demanding environment.
Automotive Industry
As the automotive industry shifts towards lightweight materials to improve fuel efficiency and reduce emissions, titanium fasteners are gaining popularity in high-performance vehicles. They are commonly used in:
- Engine Components: Bolts and nuts that hold the engine together must withstand significant forces and temperatures.
- Exhaust Systems: Titanium's resistance to heat and corrosion makes it ideal for exhaust parts.
- Suspension Systems: Reducing weight in suspension components can improve handling and performance.
Medical Field
Titanium fasteners find significant use in the medical industry, especially in surgical implants and devices. Their biocompatibility allows them to be used safely within the human body, making them ideal for:
- Bone Screws: Securely holding bone fragments together during healing.
- Joint Replacements: Fasteners used in artificial joints that require high strength and corrosion resistance.
Marine Applications
The marine industry is another major user of titanium fasteners. Because titanium resists seawater corrosion and harsh marine environments, fasteners are often used in:
- Boat and Shipbuilding: Essential for securing various components in vessels.
- Offshore Structures: Fasteners that can withstand the rigors of ocean conditions.
The Future of Titanium Fastener Manufacturing
As technology continues to advance, the future of titanium fastener manufacturing looks promising. Innovations in manufacturing processes, such as additive manufacturing (3D printing), allow for more complex designs and reduced waste. Furthermore, while the demand for lightweight and strong materials grows across industries, titanium fasteners will continue to play a pivotal role.
Moreover, the push for sustainability and environmentally friendly materials will further drive the growth of titanium as a preferred material. With its recyclability and durability, titanium aligns well with modern sustainability goals, making it a feasible long-term option for various applications.
Conclusion
In conclusion, titanium fastener manufacturers are essential contributors to the success of various industries, particularly aerospace, automotive, medical, and marine applications. Their ability to engender high-quality, durable, and customized solutions ensures that they will remain integral as industries evolve and adapt. General contractors benefit significantly from the use of titanium fasteners in their projects, leading to enhanced structural integrity, durability, and reduced overall weight. As we look to the future, titanium's unmatched properties will cement its place as a vital material in the world of fastening solutions.
For more information about the products and services offered by titanium fastener manufacturers, visit titaniumbolts.com.